Heat Treatment
Both ferrous as well as non-ferrous metals undergo heat treatment before putting them to use. Over time, a lot of different methods have been developed. Even today, metallurgists are constantly working to improve the outcomes and cost-efficiency of these processes.
For that they develop new schedules or cycles to produce a variety of grades. Each schedule refers to a different rate of heating, holding and cooling the metal. These methods, when followed meticulously, can produce metals of different standards with remarkably specific physical and chemical properties.

There are various reasons for carrying out heat treatment. Some procedures make the metal soft, while others increase hardness. They may also affect the electrical and heat conductivity of these materials.
Some heat treatment methods relieve stresses induced in earlier cold working processes. Others develop desirable chemical properties to metals. Choosing the perfect method really comes down to the type of metal and the required properties.
In some cases, a metal part may go through several heat treatment procedures. For instance, some superalloys used in the aircraft manufacturing industry may undergo up to six different heat treating steps to optimise them for the application.
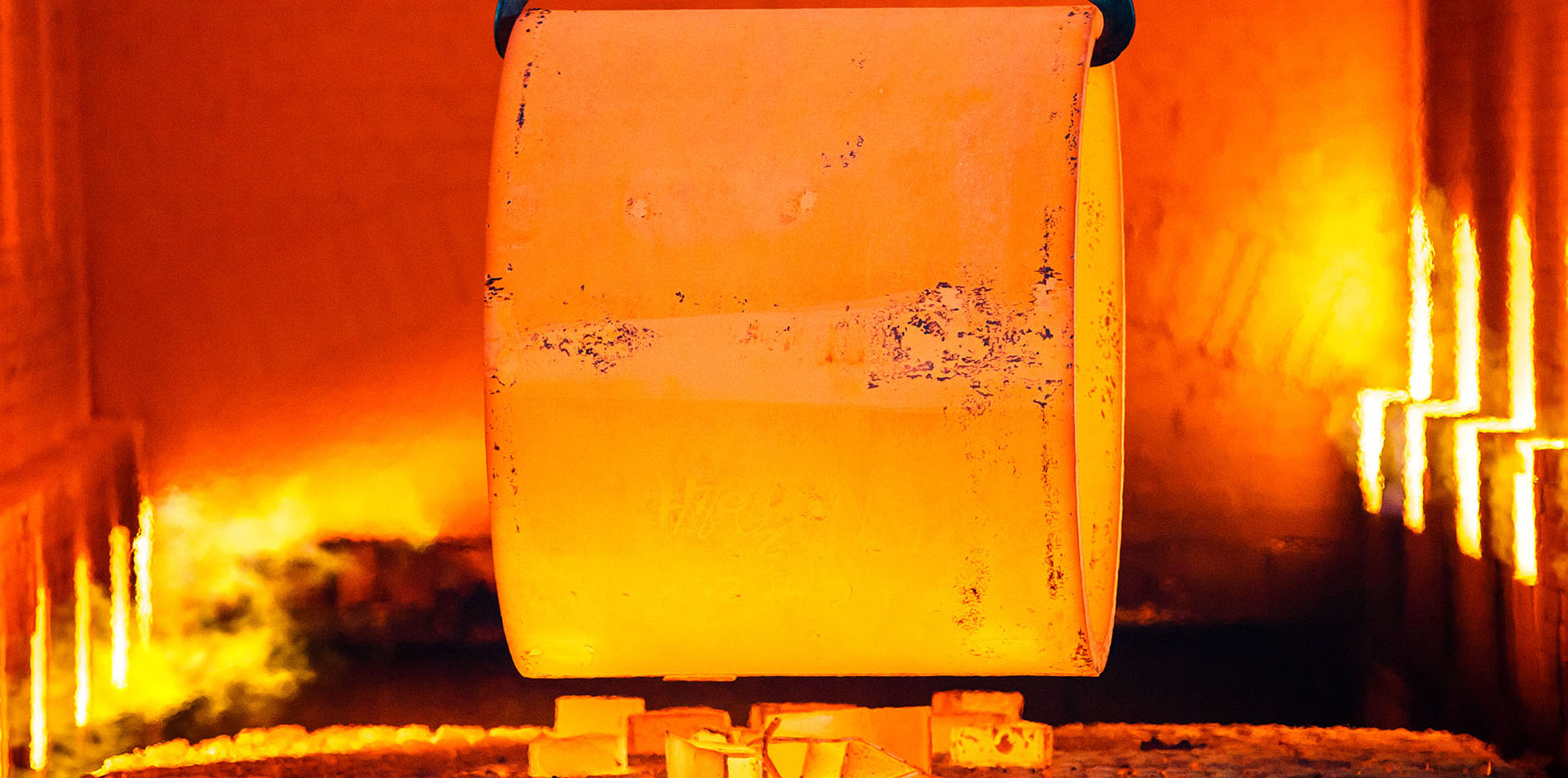