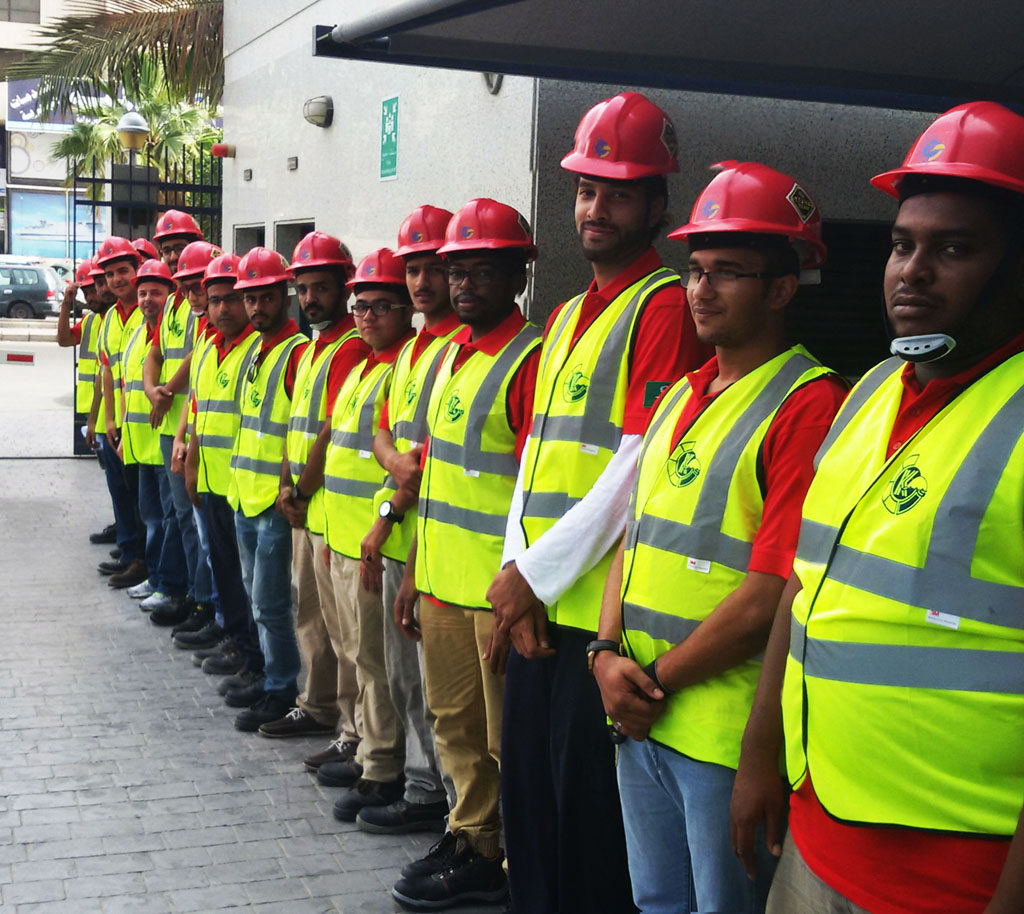
INTEGRATED MANAGEMENT
KCG’s TQM (Total Quality Management), originally implemented in 2007, is an integrative philosophy of management for continuously improving the quality of products and processes. TQM functions on the premise that the quality of products and processes is the responsibility of everyone who is involved with the creation or consumption of the products or services offered by an organization. The TQM department works hand in hand with the HSE department to capitalize on the involvement of management, workforce, suppliers, and even customers, in order to meet or exceed interested parties’ expectations.
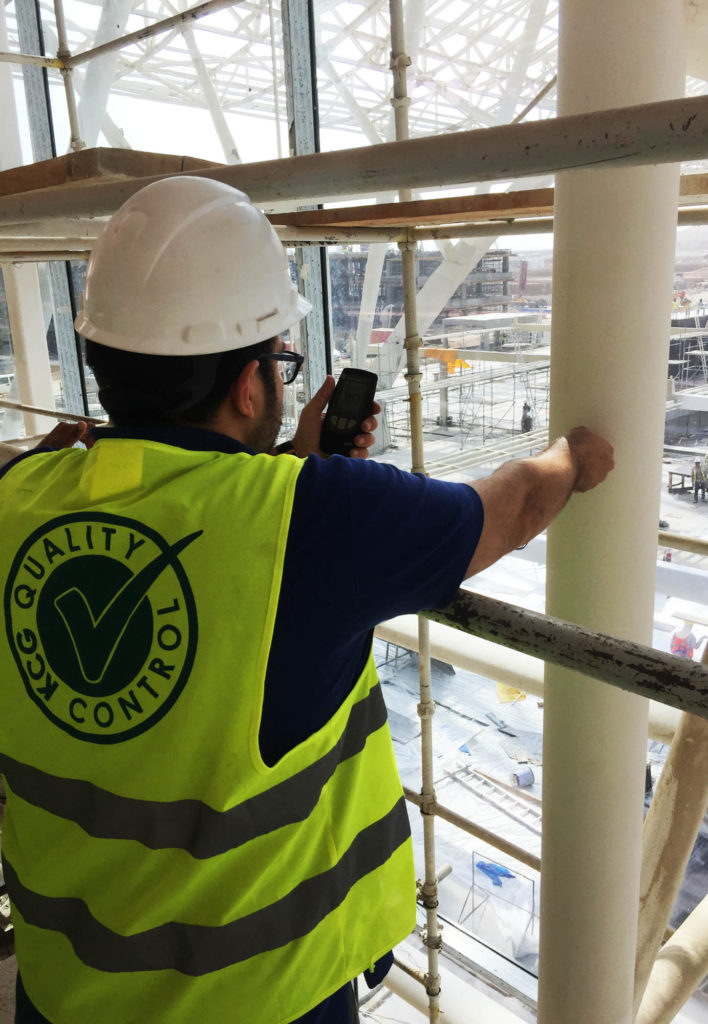
QUALITY MANAGEMENT SYSTEM
Our Quality Management System provides the tools by which we measure our performance, acting as a catalyst in promoting continuous improvement. It plays an integral part in all our day-to-day activities. We are committed to the provision of products and services that consistently meet the agreed requirements of our customers. We are certified by Bureau Veritas according to ISO 9001:2015 and we operate our business to meet or exceed those requirements.
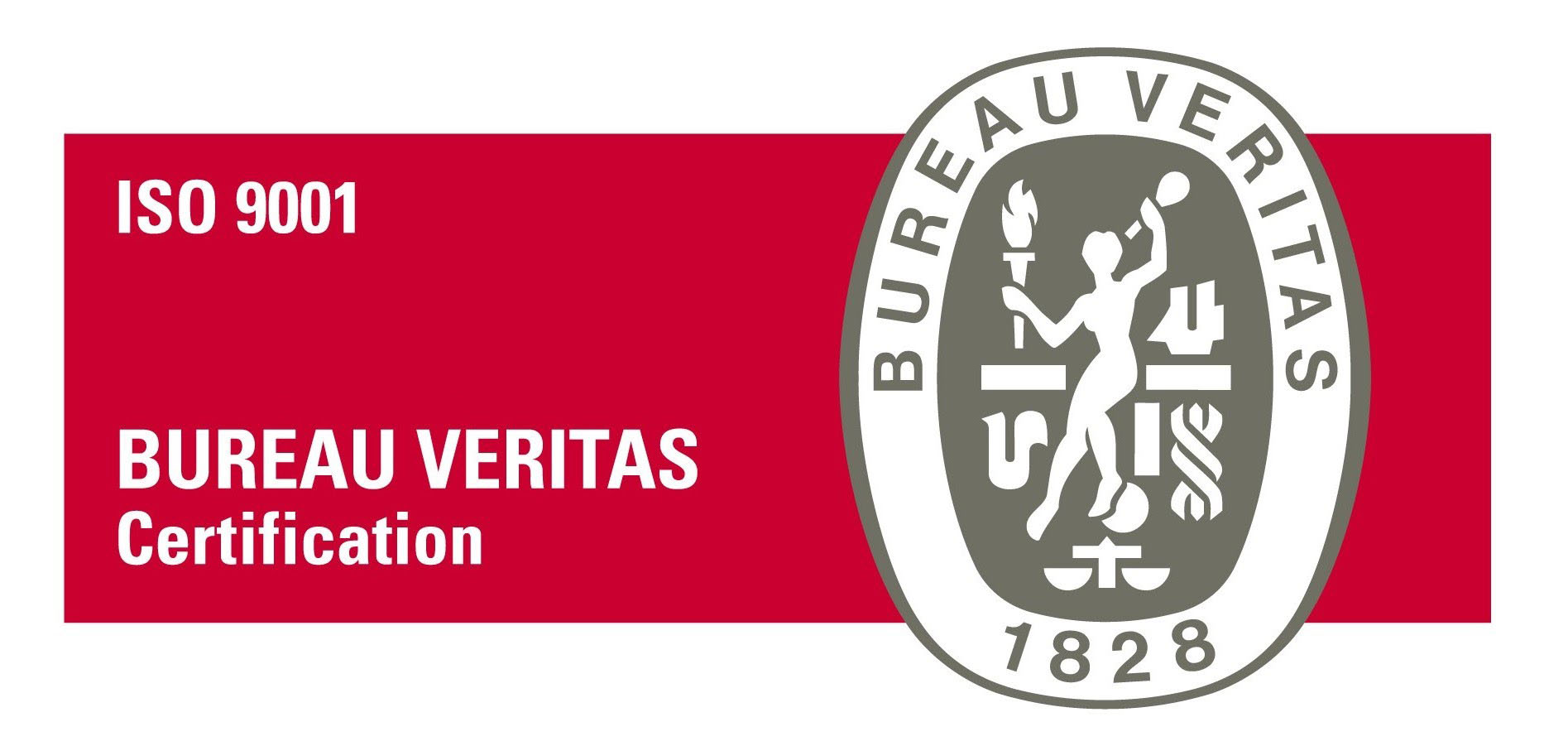
ENVIRONMENT MANAGEMENT SYSTEM
Our Environmental Management System meets the requirements of ISO14001:2015, as certified by Bureau Veritas, and ensures that we pro-actively manage our operations to minimize our impact on the environment. The key principles of our environmental management system include the identification and management of environmental risk, full compliance with environmental legislation, improvement of environmental performance to reduce impact, and the development of sustainable products and processes.
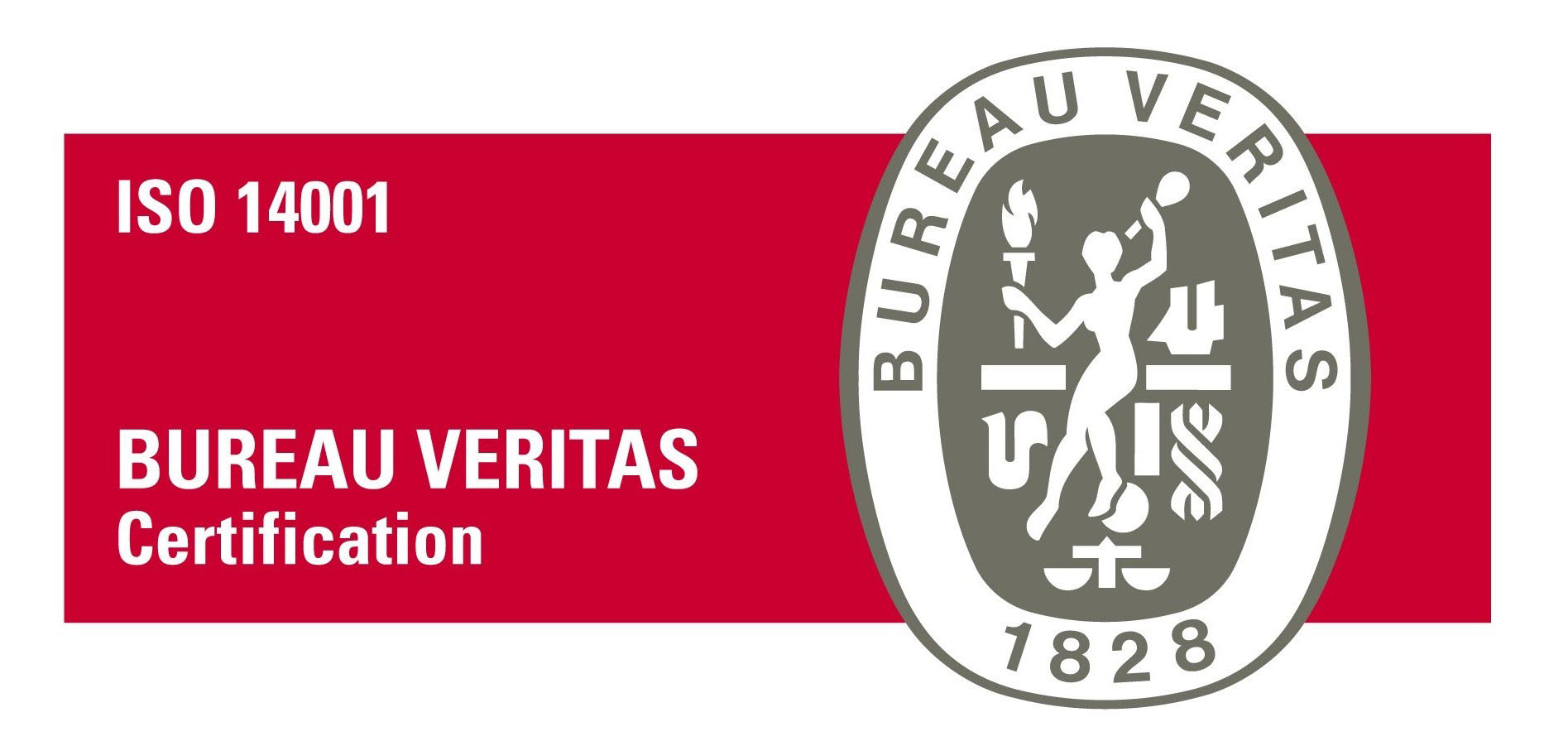
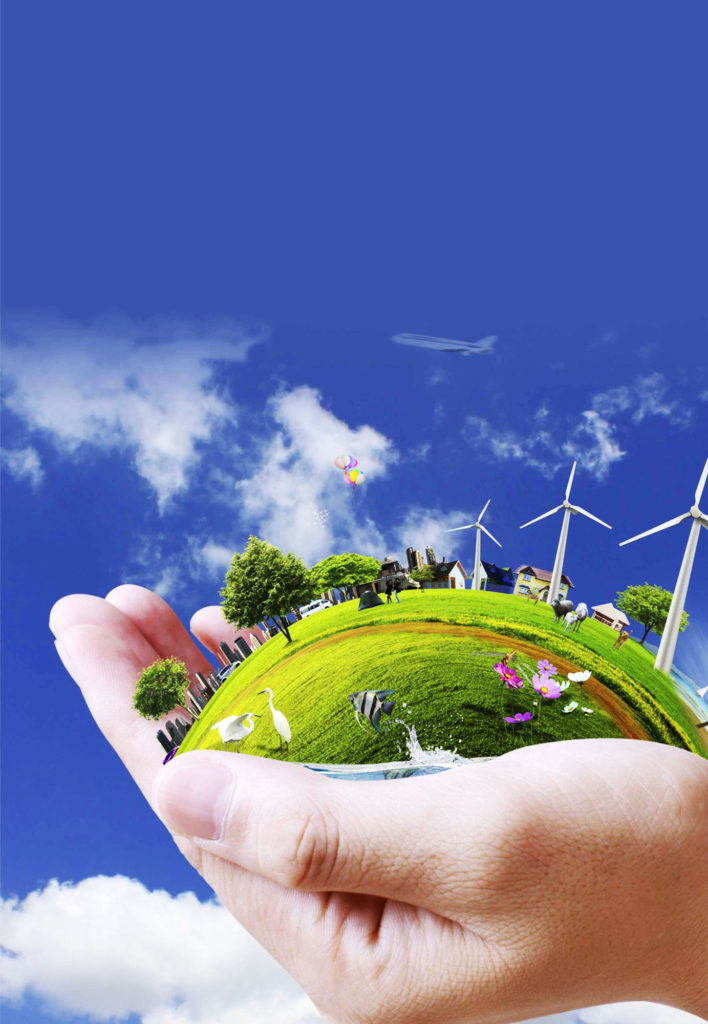
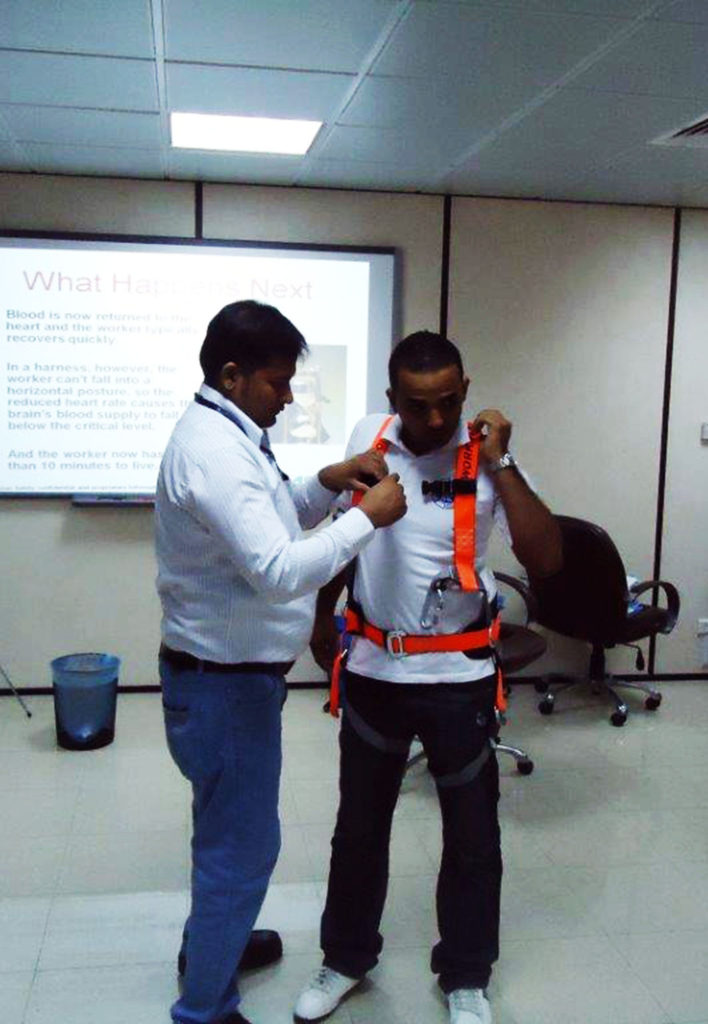
OCCUPATIONAL HEALTH & SAFETY MANAGEMENT SYSTEM
Our Occupational Health & Safety Management System promotes a safe and healthy working environment by consistently identifying and controling our health and safety risks, reducing the potential for accidents, and improving overall performance. KCG is OHSAS 45001:2018 certified by Bureau Veritas and we are consistently upholding its requirements to help the company meet its health and safety obligations in an efficient manner.
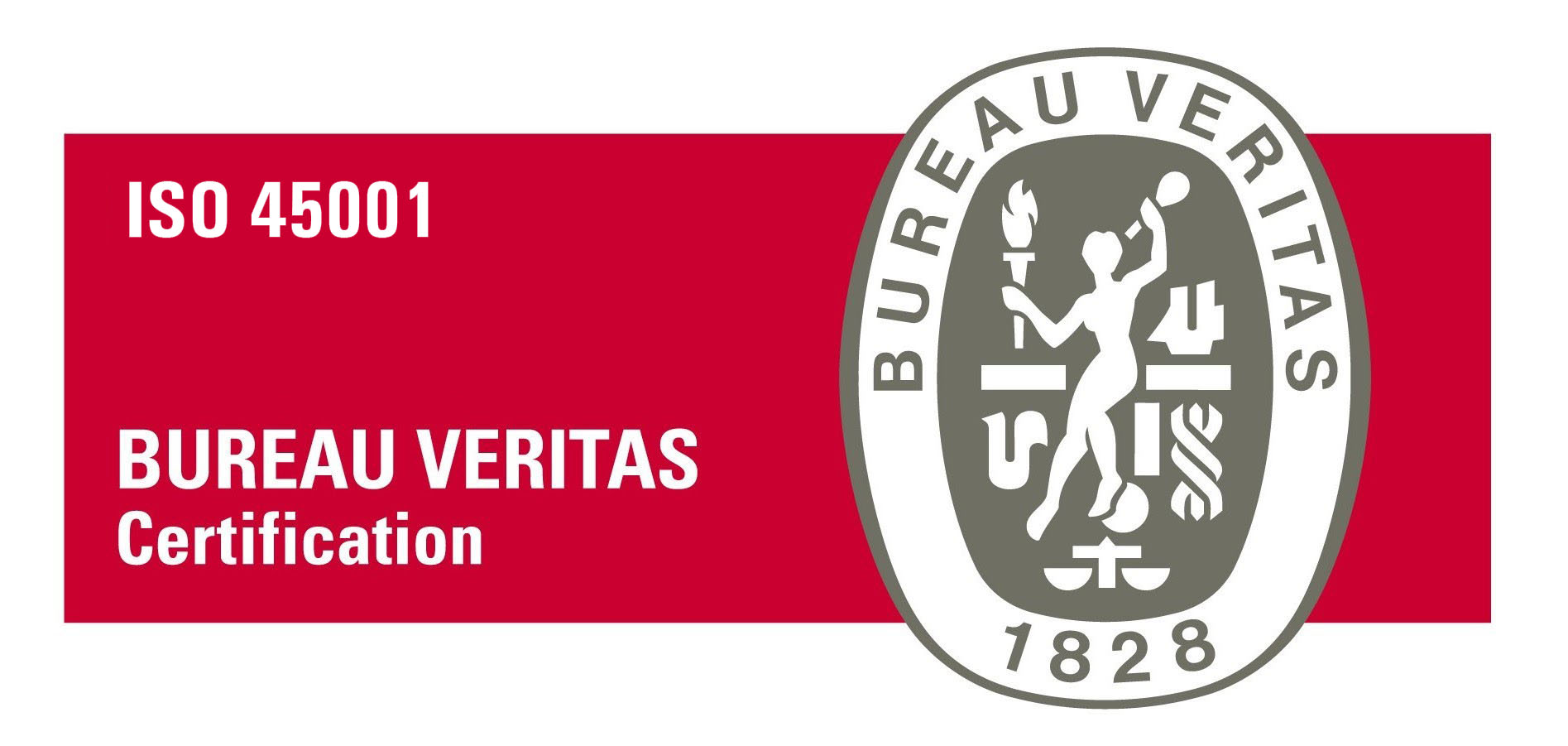
QUALITY CONTROL
To ensure our Operation System functions at its best, our quality control team monitors not only the product itself, but the way it is installed, stored and transported.
Quality control is a process designed to ensure a set level of quality standards for the products and services offered by the company. It includes the actions necessary to verify and control the quality output of products and services. The overall goal includes includes bringing name recognition for the company, and maintain its position as the market leader against the competition in the marketplace.
A quality plan is set for monitoring and controlling the process to ensure the following:
- 100% customer satisfaction
- Identifying the products and services that do not meet a company’s specified standards of quality
- Achieve Zero system defects
- Improve system installation procedures
- Abiding company’s Quality Management System requirements
- Optimizing the services results
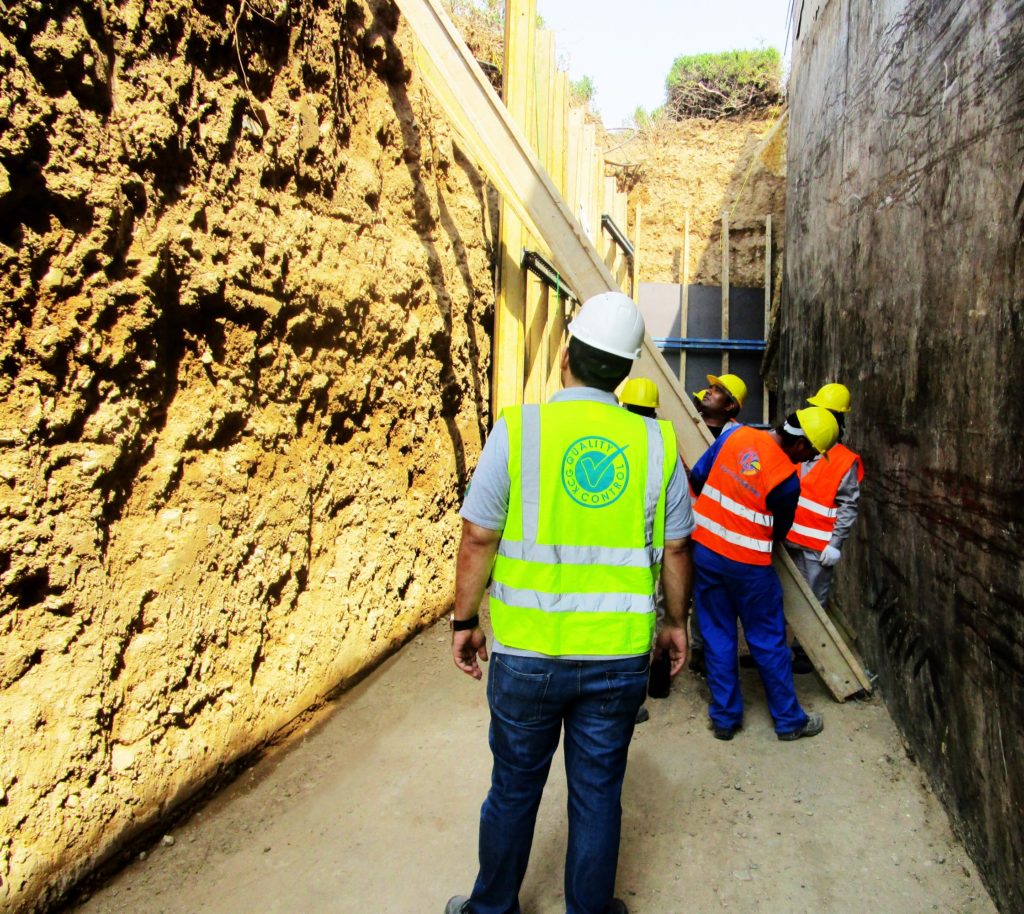
Ultimately, quality control not only consists of products and services but how well an organization works as a whole, together within the organization, and in the marketplace. A strategy to manage and improve the quality within an organization can help a company become and remain a success. Quality is an ongoing effort that must be consistent in improving every day. Every organization or business can benefit by using quality control for their products or services within the internal organization and through interactions in the marketplace.