King Abdulaziz International Airport, located in the city of Jeddah, Saudi Arabia, originally opened in 1981. Known for its Hajj terminal, an extension that was built specifically for Islamic pilgrims going to Makkah for Hajj on an annual basis, King Abdulaziz International Airport is the busiest airport in Saudi Arabia; it can handle 80,000 passengers simultaneously and has served over 30 million passengers since its inception. At 5 million square feet (460,000 square meters), the airport’s Hajj terminal, which received the Aga Khan Award for Architecture in 1983, is estimated to be among the largest air terminals worldwide. The airport is the busiest and the third largest airport in the Kingdom.
A new, revolutionary multi-stage development for the new King Abdulaziz International Airport started in 2011. The purpose of the new facilities was to increase the airport’s yearly capacity from 13 million to 80 million passengers, with a brand new terminal building, a storm water drainage network, and smart and environmentally friendly features. The new airport is expected to launch gradually over the course of four stages, with each stage seeing a yearly increase of about 20 million passengers to the airport’s annual capacity. The first phase officially launched on May 28, 2018, when the facilities successfully welcomed their first flight through one of the 6 currently functional gates. The King Abdulaziz International Airport is expected to fully launch throughout the course of the next year, with about 46 gates to be functional at time of launching.
At KCG, we are proud to say that we have contributed our services to the King Abdulaziz International Airport expansion project through 5 of our companies: CRES did repair work for concrete substrate and epoxy coating as well as cement fireproofing and internal and external protective coating, SUW installed waterproofing and thermal insulation systems, and did firestopping and traffic coating works, Structural Systems provided concrete crack repairs by injection and supply and installation of rubber type expansion joints, ACMS contributed by providing internal surface preparation for slabs and floors, reparations for the BTB terminal, and concrete leveling work, while Fulaz provided steel structures and tanks for the power generators as while as a potable water treatment plant.

The flooring works CRES contributed to the project include repair work for the concrete substrate, epoxy coating, as well as heavy duty car parking system coating, all making up for a cumulative quantity of about 500,000 square meters. The fireproofing works, on the other hand, were comprised of intumescent fireproofing, a paint-type of coating that expands when subjected to high temperatures, and cement fireproofing for steel structures with an hourly rate ranging from 1 to 3.5 hours. Total fireproofing quantities were approximately 150,000 square meters. Finally, CRES also applied protective coating, including a top coat for the steel structures in both the internal and external systems.
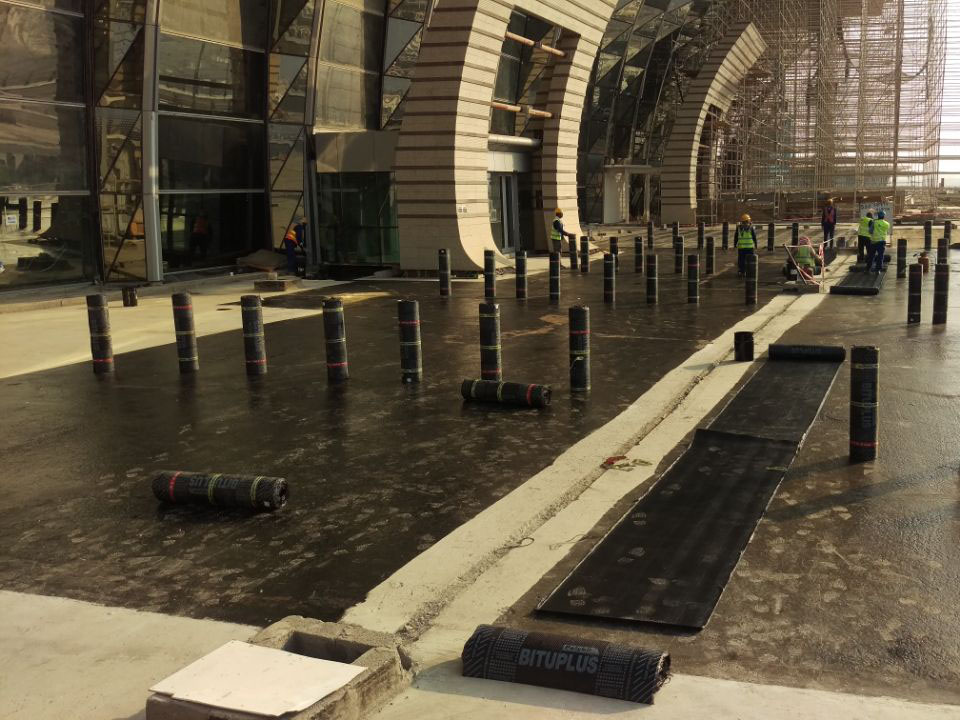
SUW’s contributions include the installation of waterproofing and thermal insulation systems for the roofs and terraces of the new facilities, waterproofing systems for all underground structures, waterproofing systems for all wet areas, firestopping works, and finally, traffic coating works for the parking structures.
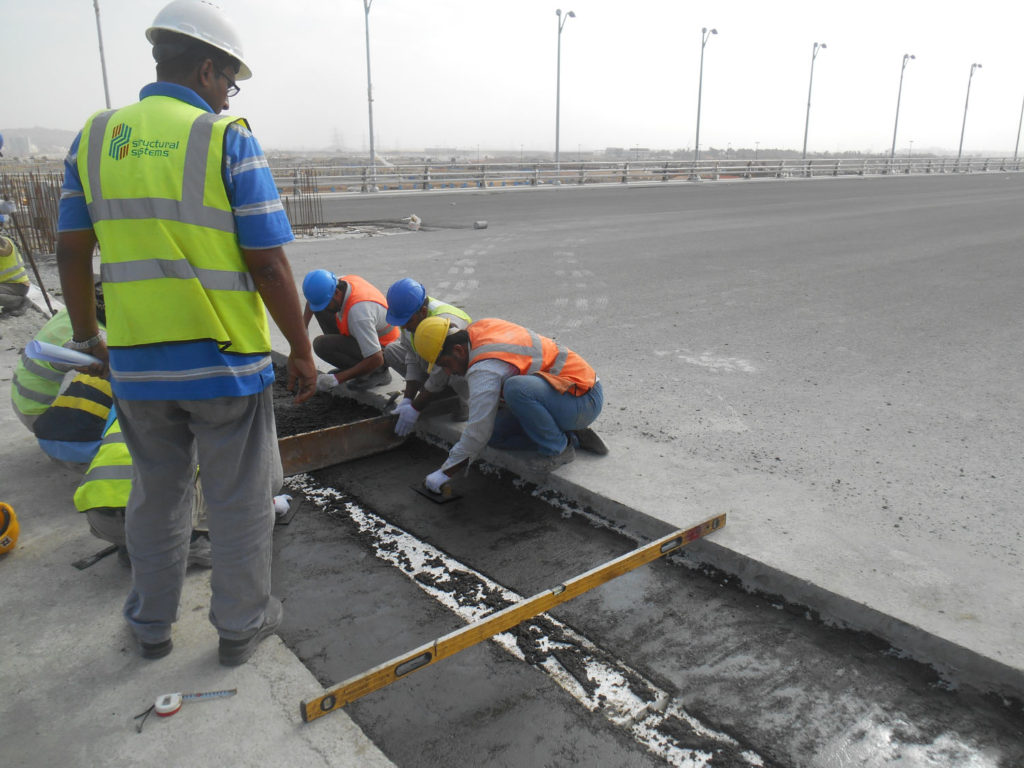
During the construction of the airport’s new car park, a slab deflection issue was noticed and quickly reported. As a result, Structural Systems was brought in to solve the issue. Structural Systems decided to treat the cracks with epoxy material that was of low viscosity and had a tensile strength of about 30 N/ mm2. Structural Systems’ second phase of work on the expansion project involved the airport’s newly constructed elevated bridges and curbside viaducts. A new rubber type of expansion joints was requested based on calculated movements on the concrete decks and, after testing, the Wabo Flex REJ (Rubber Expansion Joint) system was implemented.
ACMS, on the other hand, contributed to the King Abdulaziz International Airport project through the supply and installation of a concrete screed 15 centimeter work slab with a grade of 60,000 square meters, surface preparation work for the slabs and floors on an area of about 120,000 square meters, as well as reparations for the BTB terminal.
Last but definitely not least, Fulaz’s scope of work on the project was divided into three different areas: load center A, load center B and load center C. All areas were comprised of power generators, with each one containing a steel structure building and a diesel storage tank all provided by Fulaz. The biggest scope was that of load center C, which features the main power generator. Fulaz’s scope of work also included a potable water treatment plant to provide travelers with clean and safe water.
Construction on the new KAIA has officially been completed and 6 gates are currently functional with the rest of the gates expected to follow suit within the next year.